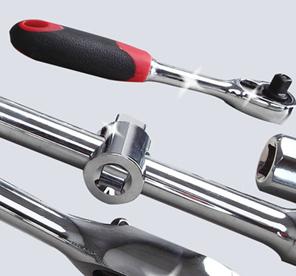
In electroplating production lines, it is necessary to perform proper degreasing of the workpiece prior to plating. Today we have come to understand the organic solvent degreasing method:
(1) Immersion method. In the dipping method, the metal material is immersed in the cleaning bath so that the entire surface is brought into contact with the organic solvent and stirred, and the grease on the surface of the base material is dissolved by the organic solvent, and the insoluble dirt is taken away at the same time. In order to increase the deoiling efficiency, it is possible to heat and lengthen the immersion time, and it is also possible to use a method of increasing the flow rate of the organic solvent. Sometimes the mechanical action of a brush or a squeegee assists the immersion cleaning to increase the degreasing speed. Various organic solvents can be used for impregnation.
(2) Spray method. The spray method uses a water pump to spray the organic solvent through the nozzle onto the surface of the metal workpiece. The grease is continuously dissolved and the dirt is also carried away. The spray is repeated until the oil is completely removed. Usually the pressure range is from 70 to 120kPa. The greater the injection pressure, the greater the proportion of mechanical detergency in the deoiling process. The impact of injection during high-pressure jet degrease is the decisive factor, and it is sprayed on the metal surface. Dust, carbon particles, quartz sand and other granular dirt have a good removal effect. In addition to volatile solvents such as gasoline, **, and methylene chloride, other organic solvents can be used in this method, but they must be handled in a closed container.
(3) Steam method. In the steam cleaning bath, the organic solvent cleaning solution is heated to form a vapor phase zone. The work piece is placed in the gas phase area, and the grease adhering to the surface is dissolved by the vapor. When the vapor is condensed by the work piece, the solvent, together with the grease, etc., falls back into the cleaning liquid below the tank body. The solvent is then heated again and vaporized into contact with the workpiece and the vapor continuously circulates. Therefore, the solvent vapor that the workpiece comes into contact with during vapor degreasing is always clean, so that the deoiling fluid can be overcome in the dipping and de-oiling process. Disadvantages of contamination and high surface cleanliness of the workpiece.
The organic solvent used for steam degreasing requires the following features:
1 has a higher ability to dissolve oil.
2 Lower heat of vaporization and specific heat capacity, the same mass of metal parts condenses the most solvent and requires the least amount of heat.
3 has a sufficiently high boiling point to ensure that the solvent vapor rinsing has a good final effect and makes the workpiece dry easily.
4 The boiling point is not so high that the solvent can be separated from the oil by simple distillation.
5 The relative density of vapor is greater than that of air, and the loss of diffusion into the air is small.
(4) Joint treatment method. The combined treatment method includes three methods of impregnating a vapor, injecting a vapor or steam, and impregnating and spraying. The degreasing effect of the combined treatment method is better. All parts with complex shapes such as deep holes, concave surfaces and old grease adherence should be used in a joint treatment method. That is, the workpiece is immersed before steam degreasing or Spray degreasing.
1 impregnated with a steam combined degreasing: that is, the workpiece is first immersed in oil and then degreasing by steam. Dirt or dirt adhesion is particularly strong parts first impregnated by degreasing, in the boiling organic solvent, the metal chips and insoluble impurities in the workpiece and most of the grease is removed; then in the lower temperature of the degreasing tank The oil is removed to remove the residual dirty solvent and cool the workpiece. Finally, the workpiece is transferred to the steam degreasing tank. Actually, the residual dirt is removed by rinsing and the workpiece is dried.
2 Injector-vapor combined degreasing: In order to improve the deoiling effect, the combination of injection degreasing and steam degreasing can also be combined. However, the composition of the degreasing device is more complicated, and the daily use maintenance and management requirements are higher than the impregnation and degreasing. After removing the oil by spraying and removing the oil by steam, the workpieces with complex shapes and old grease adhered can achieve better degreasing effect. De-oiling is usually done manually and the injection pressure is 0.
12~0.20MPa is appropriate, the nozzle position should be lower than the vapor degreasing area. Similarly, the degreasing of the workpiece by steam, and then remove the dirt by the jet to remove the dirt can also achieve a better decontamination effect.
3 Steam-immersion-injection combined degreasing: Steam-immersion-injection combined degreasing is mainly based on steam degreasing and has the advantages of impregnation, degreasing, and jet degreasing, thus ensuring that workpieces meet high cleanliness requirements. This degreasing method is highly adaptable and suitable for workpieces with complex shapes, severe surface oil contamination and mass production. The order of degreasing is to dip the oil first, then spray to remove the oil, and finally to remove the oil by steam.
The above is the method of using organic solvents to degrease the electroplating line.
Floating Sphere,Brass Solid Sphere,Cpvc Solid Sphere,Stainless Steel Solid Sphere
Antong Valve Co.,Ltd , https://www.atvalveball.com