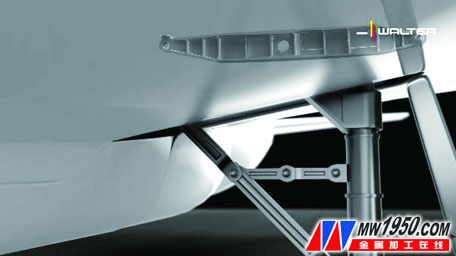
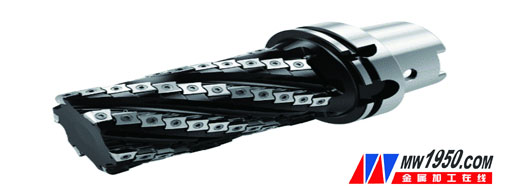
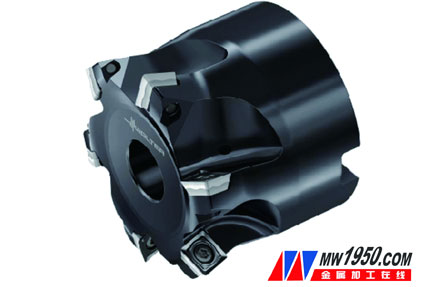
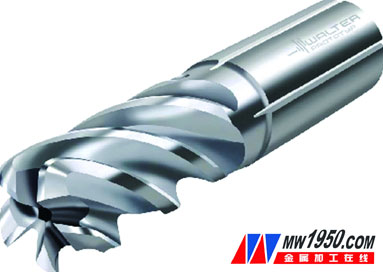
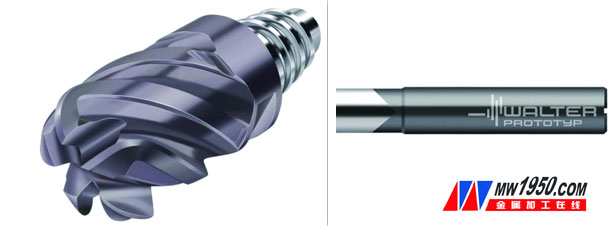
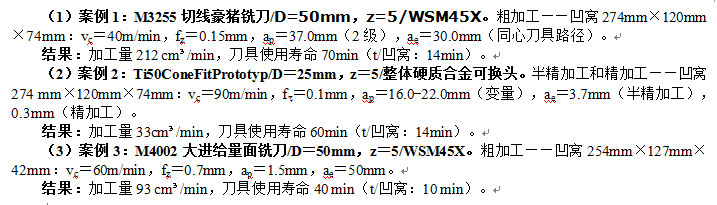
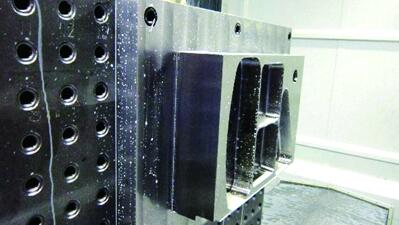
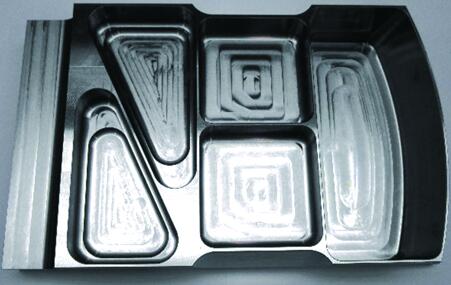
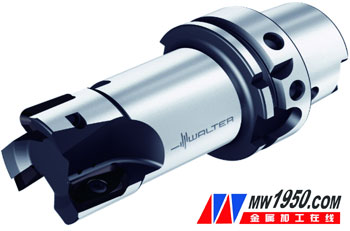
Steel Buckles With Surface Treatment
We can see buckles everywhere.
There are plastic buckles,metal buckles,small buckles,big buckles,all of them.
WinnerLifting mainly deals with Cam Buckles and some other buckles used as bag accessories.
Especially for cam buckles,they are tend to be more like industrial-using buckles,because they are of much stronger breaking strength than plastic buckles.
Sliding Buckles,Stainless Steel Buckle,D Rings,O Rings
WINNERLIFTING SAFETY EQUIPMENT CO.,LTD. , https://www.winnerlifting.com