Abstract According to the international photovoltaic technology roadmap, the battery efficiency of industrialization in the past six years (2011-2016) has increased by 0.3% per year, but it is mainly aimed at the improvement of the matte side of crystalline silicon photovoltaic cells. As the related work enters the bottleneck, the photovoltaic industry begins to pay attention...
According to the international photovoltaic technology roadmap, the battery efficiency of industrialization in the past six years (2011-2016) has increased by 0.3% per year, but it is mainly aimed at the improvement of the maternal surface of crystalline silicon photovoltaic cells. As the related work entered the bottleneck, the photovoltaic industry began to focus on the backlight of the battery, promoting the industrialization of PERC (Passivated Emitterand Rear Cell) technology. PERC battery technology can effectively improve the photoelectric conversion efficiency of solar cells. Its production and existing battery line manufacturing equipment take into account, only need to add individual equipment and processes, so it is called the "upgrade version" of the existing ordinary battery. Therefore, compared to other frontier photovoltaic technologies such as heterojunctions, PERC technology is considered to be the most reliable. With the simultaneous increase in production and efficiency of many manufacturers, 2017 will become a year of rapid growth for PERC. 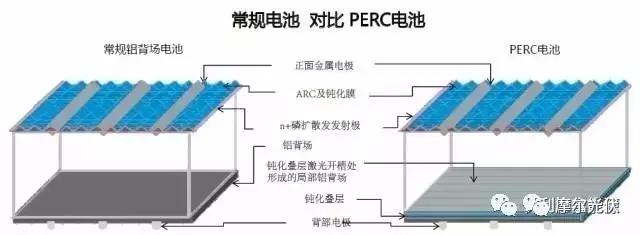
In May 2016, Jinko Energy stated that its high-efficiency polycrystalline battery using PERC and black silicon technology has entered the mass production stage, and the mass production efficiency will be increased to over 20.5% in the future.
In June 2016, Hanwha New Energy stated that its standard PERC polycrystalline components have a conversion efficiency of 19.5% and a power of 301W.
In October 2016, Trina Solar announced that its Honey Plus high-efficiency PERC battery module has an efficiency of 19.86%, setting a new world record.
At the 2016 Asian Solar Innovation and Cooperation Forum, Artes said that wet black silicon technology combined with diamond wire cutting can achieve a conversion efficiency of 19% for polycrystalline cells. Superimposed PERC technology can raise one point to 20%.
On January 17, 2017, REC Solar announced the launch of the latest Twin Peak 2 Series polycrystalline components. This component (60) with PERC technology delivers up to 295W.
Domestic first-line polycrystalline battery component manufacturers use a large number of PERC technologies to increase the efficiency of polycrystalline conversion. Taking 60 standard polycrystalline components of first-line enterprises as an example, using high-efficiency polysilicon wafer and battery process improvement, the component power can reach 275W (component conversion efficiency is 16.8%). After superimposing black silicon technology, the component power can reach 280W (component conversion efficiency 17) %), after superimposing the PERC technology, the component power can be as high as 285-290W or more (component conversion efficiency is 17.5%-18% or more).
Question 2: Why does single-crystal PERC have a capacity of 10 GW in the whole country, but in 2016, the output is only 3 GW?
Speaking of this problem, we must start from the history of single polycrystal. In fact, the crystalline silicon photovoltaic industry has only started with single crystals transferred from the semiconductor industry, and there is no polycrystalline. However, the cost of single crystal has been high and the progress has been slow. Polycrystalline has been increasing its output with large-scale ingot technology. It has gradually improved efficiency and high cost performance through high-efficiency crystal growth technology, and has always been the mainstream of the market. In 2015, single crystal began to promote diamond cutting on a large scale, and the price/performance ratio was improved.
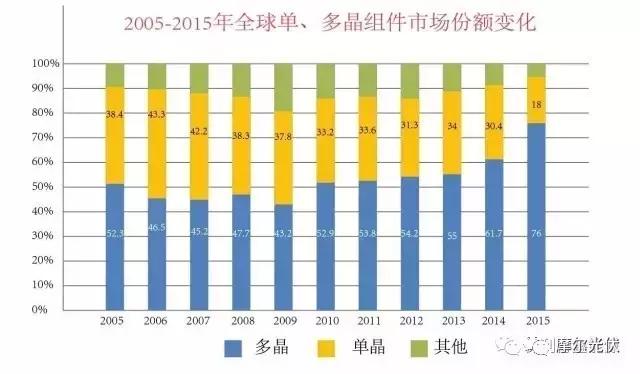
80% of the single crystal capacity can meet the requirements of the leader, and the proportion of polycrystalline can be much less. Because the front runners plan to have a low standard for single crystals, single crystal manufacturers can easily meet the requirements without adding PERC. After adding PERC technology, the cost performance is not as good as the original one, so the existing single crystal production capacity is repeatedly expanded, and the single crystal manufacturer has no power. To promote PERC technology, PERC capacity cannot be released. Another point is that although the efficiency of single crystal promotion of PERC is increased, the problem of light decay is not solved well, and it is increased in white. To solve the problem of light decay, it is necessary to increase the cost. Relatively speaking, polycrystalline is the emergence of new technologies, which has led to an increase in the proportion of the line. The original intention of the leader plan is fully reflected in the polycrystal.
The monocrystalline silicon wafers catch up with the conventional sand-cut polysilicon wafers after completing the straight-drawing multi-root and diamond-line cutting. At present, polycrystalline began to fully promote the diamond wire cutting, and supplemented with black silicon cashmere, which greatly reduced the cost and increased efficiency, and there is no new improvement point in the single crystal. At present, the price difference of single polysilicon sheet has reached 0.17 US dollars / piece, far higher than the price/performance standard value difference of 0.1 US dollars. In the future, monocrystalline products will need to increase the cost performance, and rely on new technologies to reduce costs. After all, maintaining a price difference of $0.1 is the king. Only when the price difference of a single polysilicon sheet is compressed to 0.1 US dollars/piece, the cost performance of the monocrystalline battery assembly can be revealed.
Question 3: Single crystal superimposed PERC technology "double swords combined" VS polycrystalline diamond wire cutting + black silicon + PERC "three swords combined", which is the ultimate effort?
There is a very simple calculation formula. The single crystal silicon wafer has completed the application of diamond wire cutting technology in the past two years. At present, the cost difference of ordinary high-efficiency single polycrystalline silicon wafer is about 6 hair per piece; just a large-scale mass production of diamond wire cutting polycrystalline The cost of polycrystalline silicon wafers can be reduced by another 5 hairs (the current cost reduction level is expected to continue to expand), the gap becomes 1.1 yuan; the cost of single crystal using PERC battery technology is increased by 5 hairs, and the cost of using wet black silicon wafers for polycrystalline silicon wafers is increased by 2 hairs. The cost of using PERC battery technology increased by 5 hairs, and the cost gap of single polycrystalline PERC battery became 9 hairs.
At present, the conversion efficiency of single crystal PERC battery is about 21%, the conversion efficiency of polycrystalline black silicon PERC battery is about 20%, and the efficiency difference of 1% is converted into the price/performance standard price difference of about 6 cents. In other words, single polycrystalline batteries use PERC technology, 6 hair is the price-performance standard price difference, 9 hair is the cost gap, obviously polycrystalline cost-effective.

Pvc Piled Up Door,High Speed Pvc Stacking Door,Pvc Folding Up Door,Pvc Fabric Piled Up High Speed Door
Dongguan HengTaichang Doors Co, Ltd. , https://www.dghtcdoors.com